详细介绍:
齿轮和离合器压盘都属于盘状零部件,是关系着汽车发动系统、传动系统性能的重要零部件,其铸造后的去飞边毛刺处理十分重要。市场上虽然有一些去毛刺机器,但是自动化程度低,需要大量的人工辅助,效率低,人工成本高。无法从根本上提高生产效率和产量。
2015年大连誉洋工业智能有限公司研发了一款新型的去毛刺机器,是一款五轴四联动数控打磨机床,该机床糅合当下国际上最先进的技术,赋予了机床超高的人工智能性,能够完全替代人工,全自动去除齿轮、离合器压盘铸造后的不规则飞边、毛刺、披锋;良好的硬件系统、智能软件系统相配合,赋予了设备极高的加工效率,打磨离合器压盘可达到180件/小时。大大提高铸件生产效率、产量、降低人工成本,长远来看,是最经济、省钱的去毛刺方式。
这款五轴四联动数控智能打磨机床之所以能实现对离合器压盘、齿轮等汽车铸造件的全自动去毛刺打磨,离不开以下这些先进的技术支持:
一、智能软件系统:
1、智能视觉系统——相当于人类的“眼睛”,其中集成的激光测量系统,能不断检测铸件表面、内孔各位置的尺寸、几何状态,并将数据反馈给智能控制系统;
2、智能控制系统——相当于人类的“大脑”。会根据视觉系统、各操作系统反馈的数据,进行分析、运算,实时控制,自动补偿铸件的铸造公差、加工误差,充分保证铸件去毛刺的高精度、去毛刺的一致性。
3、智能生产管理系统——能够反馈、监督整个去毛刺打磨过程,如:加工件数、加工时间、待机时间、停机原因、不合格产品报警提示….等等,为智能生产提供充分的数据支持。
4、智能离线编程平台——新类型铸件去毛刺,离线即可启动加工程序,此过程无需停机,设备能保持0停机连贯性加工,大大提高工作效率。
二、硬件系统:
1、设计了双工位工作台转换系统(主要是一个工件交换轴),使设备0停机连贯性加工,大大提高打磨效率。
为卡具设计了托盘回转装置,工件交换轴控制托盘180度旋转,4-5秒内即可实现新、旧铸件的交换,整个过程设备不需要停机,能一直保持连贯性加工。更换产品只需要更换托盘即可。替代了传统停机拆卸夹具更换铸件的方式,更加灵活、方便,可提高30%-50%的抛光效率!
2、设计了工件自转轴,可控制铸件360度自由旋转,参与插补切削,让打磨更加快捷、高效!
3、设计了大功率电主轴,转速和扭矩强劲,为铸件高效率打磨切削提供强大的动力支持!
4、采用高Dn值丝杠、高刚性导轨、高性能联轴器,保证了极高的进给速度,进给速度可达到8m/分,为铸件高效率打磨奠定了坚实基础。
5、三台电主轴——主打磨轮主轴、水平打磨主轴、铣刀主轴,复杂铸件一次性装夹即可完成所有部位的去毛刺打磨,减少换刀时间,节省节拍。
6、采用自动排屑系统和安全光栅——通过自动排屑系统可将打磨产生的金属屑排放到指定位置,减少人工清理,保证车间0粉尘污染;安全光栅,高度灵敏,当人触及安全区域时,设备会受到感应及时停机,保障车间人员的人身安全!非常节能、环保、安全可靠!
在以上先进智能的软件系统、硬件系统的支持下,誉洋数控去毛刺智能打磨机床具有以下不可超越的优势:
1、 可实现全自动去毛刺打磨、只需1人辅助即可,同时1人可以操作多台设备,降低人工成本、彻底杜绝人为不稳定影响因素。
2、 超高打磨效率,打磨离合器压盘180件/小时,20秒/件,打磨差速器壳体90件/小时,是人工的5-10倍。
3、 超高人工智能性,一边打磨,一边自动补偿各种误差(铸件铸造误差、加工误差、磨轮状态),充分保障了去毛刺高精度!
4、 全自动、多方位智能打磨,铸件表面、内孔、沟槽、凹槽、死角、盲孔、交叉孔……等各个位置的毛刺都可有效去除。
5、 离线编程,适合多种类、多种规格的铸件去毛刺使用,真正的一机多用!
6、 设备具有高刚性,又采用大功率电主轴,可以以极高的效率打磨高硬度铸件,如:铸钢、铸铁、球墨铸铁、合金铸铁、灰口铸铁、合金钢、锰钢、碳钢等等。
7、 打磨工具采用金刚石磨轮和树脂砂轮片,平均使用寿命为3-6个月,耐磨耐用,大大降低单个铸件的打磨成本!批量铸件去毛刺,更经济、省钱!
适用范围:离合器压盘、齿轮、凸轮轴、涡轮壳、曲轴、排气管、转向臂……等汽车铸造件;高铁、船舶、航空、农机、建筑机械、矿山机械铸件;卫浴洁具制品、五金件、手机平板电脑金属壳;其他各种锻件、冲压件、压铸件。
如果您对设备感兴趣,可以把您的产品图片或模型、参数发过来,我们会根据您的去毛刺需求、加工节拍等制定自动化去毛刺方案,以视频的形式发送给您,让您提前了解去毛刺原理、流程。咨询电话:4008773838,网站:http://www.yuyangrobot.com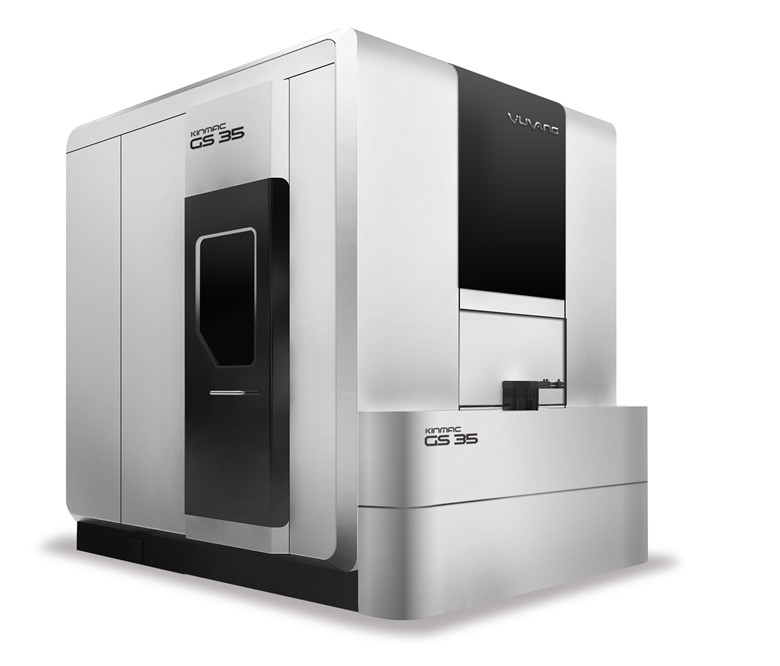
|